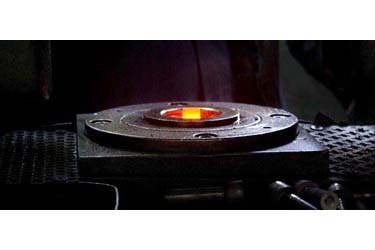
Forgings and precise machining of brass, aluminium and copper.
Early stage engineering |
The design conference |
Material selection
Part configuration |
Dimensional tollerances |
Applying guidelines
Surface finishing and coatings |
Ispection and testing |
Delivery
An experienced and capable forging company engineer should be able to make design suggestions to consolidate components, simplify processing, reduce required machining, speed delivery and so on. It may be possible to achieve forging’s high-level performance benefits without significantly increasing material or production costs over those associated with other processes.
The key is to get the forger involved early. The benefit derived from consultation will vary with the complexity of the part and the forging process involved. For instance, impression die forgings may benefit somewhat more dramatically than open die products.
However, the ideal first step toward getting the most from a forged part is to form a team consisting of the product's designer, the purchasing manager and a quality control or manufacturing representative. Then this team should sit down with a technical representative of our forging company while the product or component design is still being evaluated.
The focal point in these early meetings with candidate forgers should be an engineering drawing. The part print should be fully detailed, showing finished dimensions and tolerances. If the forging is to be delivered in a rough-machined or as forged state, the required machining envelope should be clearly specified. In many cases, it can be advantageous to provide a drawing that shows how the forged part will mate with other components in the finished assembly.
Another critical part of these early design meetings should be the service requirements of the application. The forger needs complete information on how the forging will be used, the operating environment, and critical mechanical properties. A thorough understanding of service stresses – load-bearing, power transmitting, impact, hydraulic pressure, high or low temperatures, corrosive conditions – and the stress location can allow the forging engineer to make design and process suggestions that can result in an improved product and reduced manufacturing costs.
-
A partner ready to listen and able to advice
Pe Giovanni di Pe Franco e C. S.a.s. - Via del Bosco, 10/A i-25076 Odolo (Brescia) Italy
Phone: +39 0365 82 65 18 - Fax: +39 0365 82 69 52 - Email: info@pegiovanni.com