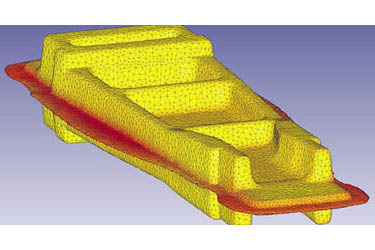
Forgings and precise machining of brass, aluminium and copper.
Early stage engineering |
The design conference |
Material selection
Part configuration |
Dimensional tollerances |
Applying guidelines
Surface finishing and coatings |
Ispection and testing |
Delivery
Close cooperation between buyers and producers of forgings has always been a vital part of virtually achieving the best possible product at the lowest possible cost. With major advances in forging methods and materials improvements, this collaboration is more critical than ever before. By keeping abreast of these advances, and working closely with the forger, the engineer or buyer can ensure delivery of high-quality products with important cost savings.
Despite its long history and the many technological developments that have taken place in recent years, forging still involves a good deal of artistry. Even as product designers and industrial buyers learn more about shaping of metals, there is still much to be gained from bringing the forger into the design and specification phases of product development.
Of course, such basic questions as whether a given part can or should be forged must be addressed at an early stage. There are many instances when any of several processes can be used to produce the component in question.
Once it has been determined that a product or component requires the strength, toughness, dimensional accuracy and overall integrity of forging, there is still the question of which forging process is most appropriate. Usually, this decision is straightforward, based on part, size, configuration and quantity required.
However, to help in those situations when the choice is not so clear cut, the forging buyer should have at least a general knowledge of methods and equipment used in the industry. Besides a general knowledge of forging, buyers should also have a clear idea of what they specifically require and how readily individual forgers can meet their needs, because capabilities can vary dramatically from one company to another.
For instance:
• Does the forger have experience in applications similar to the one being considered?
• Is design assistance offered?
• Does the forger have the equipment required to produce the part?
• Is the forger able to provide related services like heat treating, machining, testing and so on?
• Is the supplier accustomed to producing the volume required? Does the company specialize in long runs, short runs or quick delivery?
• Does the supplier have a cutting-edge internal tool shop and/or metrologic lab?
The answers to these and other questions will help narrow the field to a few qualified forgers and here at Pe Giovanni we know very well how important are these aspects and we let our customers take advantage of the valuable technical and design assistance available from our forging and machining experts cooperating to plan together since the early stage.
-
State-of-the-art internal tool shop and metrologic lab
Pe Giovanni di Pe Franco e C. S.a.s. - Via del Bosco, 10/A i-25076 Odolo (Brescia) Italy
Phone: +39 0365 82 65 18 - Fax: +39 0365 82 69 52 - Email: info@pegiovanni.com